

Wiggling the handle of the parting tool left to right as I make the cut provides clearance for the tool as it penetrates deeper into the blank. The finished dimension is 7/8″ (22mm), so 1″ leaves room for perfecting the curve. With a caliper set to 1″ and a parting tool, I cut a groove into the blank to the target depth where the waist will narrow. Use the dimensions shown in the Drawing to lay out the locations of the bottom and the widest diameter of the holder. The next step is to establish the form for the toothpick holder. Clear the waste from the hole frequently to eliminate binding, reduce friction, and produce a clean, centered hole.Īfter drilling the center hole, remount the live center and bring up the tailstock for added support.įorm the Body Use a parting tool and caliper to establish the waist of the form and locate the base. I set the lathe to 700 rpm and use a 1″ (25mm) Forstner bit mounted in a drill chuck with a drawbar to drill the center hole. A standard toothpick is 2-1/2″ (6cm) long, so a 1-1/2″- (38mm-) deep hole fulfills the need. The hole in the toothpick holder should be deep enough that the toothpicks stand upright, but not so deep that the toothpicks are hidden. Greater mass in the blank makes drilling safer. The center hole is drilled prior to forming the outside shape. This provides additional support, ensuring the blank will continue to run true when you are shaping the outside.ĭrill the Center Hole The author uses a drill chuck and drawbar setup to hollow the form. Use the handwheel on the tailstock to snug the live center until it exerts firm - but not excessive - pressure on the blank. This sequence assures that the cylinder runs true. Bring up the tailstock with the live center at the marked center point and finish tightening the jaws. Remove the blank from between centers and mount it loosely in your chuck. Mount the blank in the scroll chuck, using the tailstock to center the blank and provide support while turning. The step wall, or shoulder, needs to be crisp and true for the jaws to have maximum holding power. For a solid hold, the bottom of the tenon must not touch the bottom of the jaws. For a project of this size, a smaller chuck will work well size the tenon to fit your chuck jaws.

Use a parting tool to create a tenon at one end of the cylinder. Create a tenon on the bottom end to fit your scroll chuck jaws. Better that a few flat spots remain than have a cylinder that is too small. Turn away only enough wood to create a round cylinder.

Mount the blank on the lathe between centers and use a spindle-roughing gouge to turn the blank round. The indentations make registering the drive and tail center spurs easier. Mark the center point on each end of the blank using a center punch or awl. Locate the centers on each end of the blank and use an awl or punch to reference each location. The Drawing shows the dimensions of both the rough blank and the completed form.
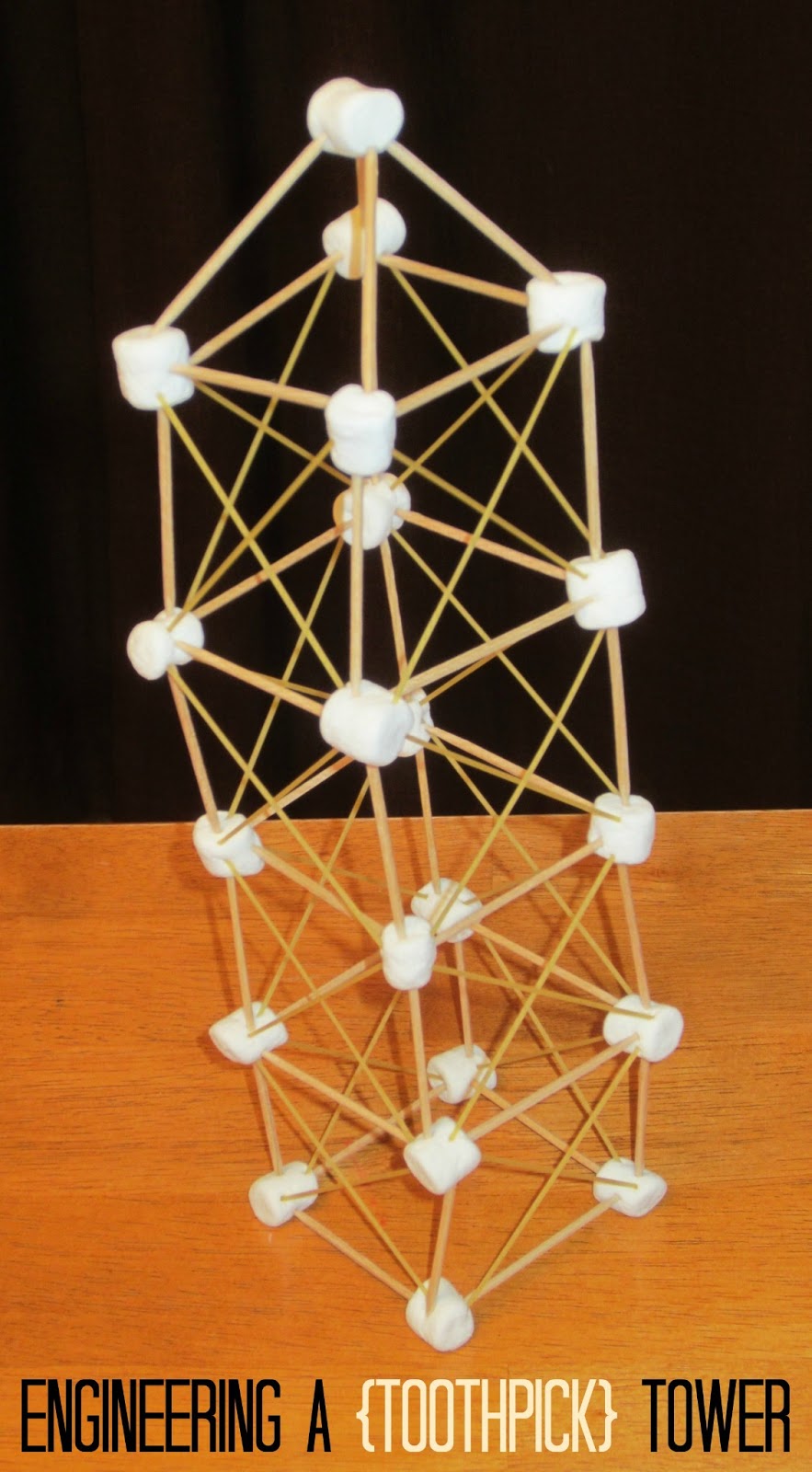
I typically start with a blank of hard maple or cherry 1-3/4″ (4cm) square and 6″ (15cm) long. The wood must be seasoned and the blank square and true on all four sides. The wood can be any species of dry wood or a blank that has been glued up of contrasting colors. First cut from B to A, then B to C, then D to C, always from large diameter to small. Note the arrows indicating cutting direction for shaping the exterior. Rough the Blank Completed dimensions for the toothpick holder. His toothpick holder is useful in today’s homes, little wood is needed, one can be completed in an hour, it is turned between centers and in a chuck with tailstock support (reducing the risk of the blank flying off the lathe), and it allows for some design creativity. I had been casting about for an ideal first project when a fellow turner, Jeff King, showed me his toothpick holders. A honey dipper, muddler, or candlestick holder are frequently the objects of first efforts, but another good choice - and one with daily usefulness - is a toothpick holder. This article, “Turn a Toothpick Holder,” is from the pages of American Woodturner and is brought to you by the America Association of Woodturners (AAW) in partnership with Woodworker’s Journal.Ī functional first project will continue to remind a turner of the joy of woodturning for many years.
